Introduction to Double Stage Crusher
Double stage crusher, also known as double rotor hammer crusher, is a new type of raw material crusher. This machine overcomes the defects of high moisture content in raw materials that bind to the bottom of the grate and are difficult to discharge. It has the advantages of high production efficiency and good crushing effect. This machine is suitable for crushing materials such as calcite, limestone, coal slag, slag, shale, coal gangue, construction waste, and construction waste in brick and tile factories, solving the problem of using gangue and coal slag as additives and internal fuel in brick factories; The challenge of crushing high moisture materials for producing standard bricks and hollow bricks using gangue and shale. This machine is equivalent to two hammers combined into one, reasonably combined into a whole, with two sets of rotors connected in series for use.
Performance advantages of two-stage crusher
1. This series of crushers uses dual rotors and two continuous crushing processes, without a screening device. All kinds of wet slag can be crushed, and can be removed from the water or crushed at any time without any bonding or blockage. To control the size of the material, simply adjust the gap between the crushing hammers. Generally, crushers cause blockage due to material retention in the crushing chamber, leading to increased wear and tear of related components. This series of crushers can avoid the above phenomenon.
2. High alloy wear-resistant hammer head. Hammer head and handle combination use, only replace the hammer head, not the handle.
3. Unique displacement gap adjustment technology, the hammer head does not need to be repaired after wear and tear, and can be repeatedly used to move the position. One set of hammer heads can support three sets of hammer heads for use.
4. The crusher rotates in both directions, and through continuous equal shift bidirectional operation, the hammer head and crushing gear plate can wear evenly, reducing the frequency of downtime for replacing vulnerable parts.
5. Suitable for fine crushing of brittle materials, non clogging, low dust, and low noise.
6. Easy installation greatly improves the freedom of the equipment.
7. Quick maintenance, the side doors on the upper side of the crusher can be opened in reverse, making the maintenance and replacement of vulnerable parts of the crusher faster and more convenient, shortening the maintenance time.
Working principle of dual level broken shorthand
During the two-stage crushing operation, driven by dual motors, the two sets of rotors connected in series rotate at high speed simultaneously. The material is immediately crushed by the hammer head of the rapidly rotating lower rotor in the machine cavity after being crushed by the upper rotor. The materials in the cavity collide and crush each other at high speed, achieving the effect of hammer powder and material powder, forming coal slag particles with a discharge particle size of less than 3 millimeters. This particle size can fully meet the requirements of brick and tile manufacturers as internal combustion bricks.
Technical parameters of two-stage crusher
specifications | ZPCΦ600×600 | ZPCΦ800×600 | ZPCΦ1000×800 | ZPCΦ1200×1000 | ZPCΦ1400×1200 | ZPCΦ1600×1400 |
Feed particle size (mm) | ≤100 | ≤120 | ≤160 | ≤200 | ≤200 | ≤200 |
Discharge particle size (mm) | ≤ 3 (adjustable) | ≤ 3 (adjustable) | ≤ 3 (adjustable) | ≤ 3 (adjustable) | ≤ 3 (adjustable) | ≤ 3 (adjustable) |
Production capacity (t/h) | 20-30 | 35-55 | 60-90 | 80-120 | 100-140 | 120-180 |
Motor Power | 22KW×2 | 45KW+55KW | 55KW+75KW | 90KW+110KW | 132KW+160KW | 160KW+200KW |
Material moisture content | No requirements | No requirements | No requirements | No requirements | No requirements | No requirements |
Dimensions (length x width x height) (mm) | 2300×6500×1680 | 2500×870×1700 | 3500×8702×1800 | 3800×1800×2400 | 4400×2300×2600 | 4400×2300×2600 |
Delivery site
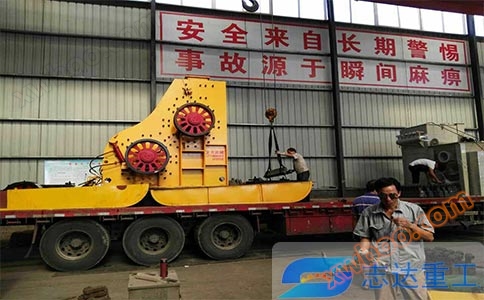
Double stage crusher delivery site